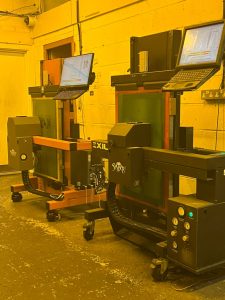
The first SPYDER III computer to screen installation has been completed at London-based T shirt specialist Fresh Air.
EXILE Technologies officially launched the long awaited SPYDER III in the UK at Printwear & Promotion LIVE! in February.
With a new 1200dpi Xerox industrial print head the SPYDER III sets a new benchmark for ink jet CtS imaging that can rival direct laser exposure systems for screen stencil quality. Unlike a direct exposure system, the SPYDER III can be used with any type of emulsion, without compromising imaging speed.
The SPYDER III produces a typical T shirt screen stencil in 60 seconds or less and is set to become the new industry standard for textile and transfer screen printers who want to eliminate film and produce higher quality screen stencils.
Fresh Air is one of the biggest garment screen printers in the UK – with nine automatic presses and the ability to print up to 40,000 garments per day. In busy periods the need to produce 200 or more screens a day is not uncommon. Fresh Air’s owner, Lee Craze had been looking at supplementing their existing SPYDER II system, which has been running the bulk of Fresh Air’s screen making since March 2018. Mr Craze looked closely at the latest direct laser exposure (DLE) systems before deciding on a second SPYDER system, this time the new higher resolution SPYDER III.
He said: “The DLE systems look great on paper but cannot match the SPYDER systems for imaging speed, even when you use the manufacturers recommended fast exposure emulsions, which carry a price premium. We were very happy with our existing emulsion choices and the new SPYDER III gives us the ability to run higher screen rulings to boost our stencil image quality.”
The SPYDER III CtS system is available with conventional tri-lock mechanical registration systems, or an optional MHM compatible pin registration. Artwork is applied and positioned digitally, with .01% accuracy, directly on to a coated screen. This eliminates the need for manual and labour-intensive film registration thereby streamlining the entire screen preparation process. The combination of mechanical registration and digital image placement eliminates any human error associated with manual film placement and translates into significant reductions in press setup up times and dramatic increases in screen-room productivity.
The stencil is printed directly onto a coated screen and after imaging the screen is ready for immediate exposure on the optional V-LUX UV-LED Exposure system, without the need for a glass or vacuum.
Pin-holing is therefore completely eliminated and because the stencil is ‘bonded’ to the emulsion there is no undercutting of the stencil so small highlight detail is retained. After exposure the water-soluble wax washes off quickly and easily along with the unexposed emulsion.