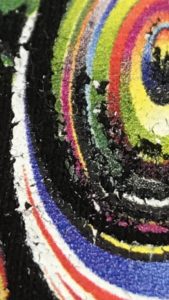
This month read all about top tips for using a tunnel dryer, curing and rip testing from Colin Marsh, managing director of Resolute DTG.
As the use of DTG printing is constantly on the increase, the volume of shirts produced with the DTG process naturally grows. In high volume environments tunnel drying your DTG prints can increase production and in some cases, reduce power consumption. But there can be pitfalls to look out for.
Before the release of fast curing DTG inks the normal cure time for a small to medium format DTG print in a tunnel dryer or heat press was around three minutes. Some high end DTG processes can take up to seven minutes and require very large dryers. Using a standard tunnel dryer designed for screen printing is possible, but as most screen printed T shirts cure much faster than DTG prints, most dryers were designed with this in mind.
Faster curing ink benefits
With the recent advance in DTG inks, most of the modern formulations now cure in around 60 seconds, some even cure in as little as 35 seconds. With these vastly reduced cure times it is now much easier to use a tunnel dryer with the added benefit of a smaller less expensive dryer capable of doing a good job. This allows DTG businesses running multiple printers to streamline the curing process and very often reduce labour costs. You will of course pay more for a tunnel dryer than most heat presses, but the ROI is very quick, often only a few months in the right circumstances.
The faster curing DTG inks do speed up production reducing bottle necks at the heat press, but fast curing DTG’s ink have another advantage up their sleeve. With a reduced cure time the fibres in cotton T shirts do not get as damaged. Long periods of heat and zero moisture content can make the fabric brittle and this leads to the garment tearing very easily. Once cotton is damaged by heat there is nothing you can do to increase its durability.
Is pre-treatment and curing damaging my shirts?
If your DTG shirts are tearing after curing there is a simple elimination test you can do. In many cases the pre-treatment and printing process is blamed for shirts tearing easily after being printed then cured.
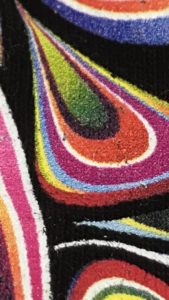
Older formulations if used incorrectly could in fact do this but thankfully most of today’s pre-treatments work in the opposite way. A good pre-treatment can in fact make a T shirt more durable and less susceptible to tearing, as long as the heat used to cure it is correct and not too much for the shirt in general.
A simple test if you are using a heat press is to cure the sleeve of a T shirt, with no print or pre-treatment. Now cure the printed section of the shirt and let it cool down. Rip test both parts and you should get a similar resistance from both parts of the shirt before tearing. If you are using a tunnel dryer any non-printed/pre-treated area of a cured shirt can be tested in this way.
How can I tell if my prints are cured correctly?
Washing the printed garment is the only true way to see if the cure is correct. It is quite common to see wash tests being performed on a weekly and sometimes daily basis during busy periods.
To demonstrate the visual symptoms, I have included two pictures. One is of an under cured T shirt after one wash and the other is of a T shirt cured on a small tunnel dryer correctly after 10 washes. Both were produced on the same DTG printer and using the same t-shirt, pre-treatment, ink, artwork and print settings. The dryer used was quite small with a chamber measuring only 80cm and running on a standard 13 amp socket.